
Prioritizing root causes based on their impact on performance Verifying root causes through data analysis Analyzing data using statistical tools and techniques The Analyze phase involves identifying the root causes of problems and determining their impact on process performance. The Measure phase involves collecting data to establish a baseline for the current process performance. Establishing project objectives and success criteria The Define phase involves establishing the project scope, objectives, and customer requirements. The DMAIC (Define, Measure, Analyze, Improve, Control) process is a structured, data-driven methodology used in Lean Six Sigma to guide project teams through problem-solving and process improvement. Participating in project reviews and continuous improvement efforts Facilitating communication between project teams and stakeholders Assisting with data collection and analysis Green Belts are part-time project leaders who support Black Belts in executing Lean Six Sigma projects. Reporting project progress and results to Champions and executive leadership Ensuring project milestones and objectives are met Applying Lean Six Sigma tools and techniques to identify and eliminate root causes of problems Facilitating the sharing of best practices and lessons learnedīlack Belts are full-time project leaders responsible for executing Lean Six Sigma projects. Assisting with project selection and scoping Developing and delivering training programs Providing technical expertise and guidance on Lean Six Sigma tools and techniques Master Black Belts are experts in Lean Six Sigma methodology, responsible for training, coaching, and mentoring Black Belts and Green Belts. Communicating project progress and results to executive leadership Removing barriers and ensuring project success Providing support and guidance to project teams Identifying and prioritizing potential projects Ensuring alignment of Lean Six Sigma initiatives with organizational goalsĬhampions are high-level leaders responsible for overseeing Lean Six Sigma projects within their respective departments or business units. Communicating the importance of Lean Six Sigma to the organization Allocating resources, such as funding and personnel Establishing a vision for continuous improvement The executive leadership team is responsible for setting the strategic direction and providing resources for Lean Six Sigma initiatives. These roles help ensure a structured approach to problem-solving and process improvement. In a Lean Six Sigma organization, various roles and responsibilities are assigned to team members. Lean Six Sigma Roles and Responsibilities Enhanced employee engagement: Lean Six Sigma empowers employees to identify and solve problems, fostering a culture of continuous improvement.Faster time-to-market: Streamlined processes result in quicker product and service delivery.
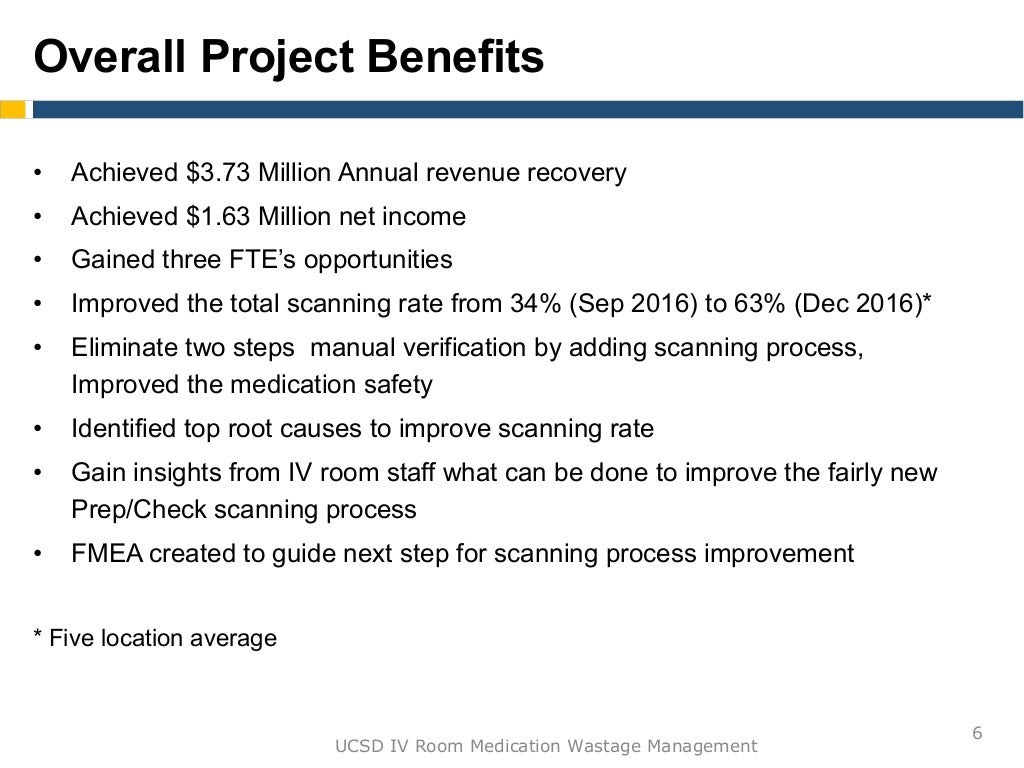
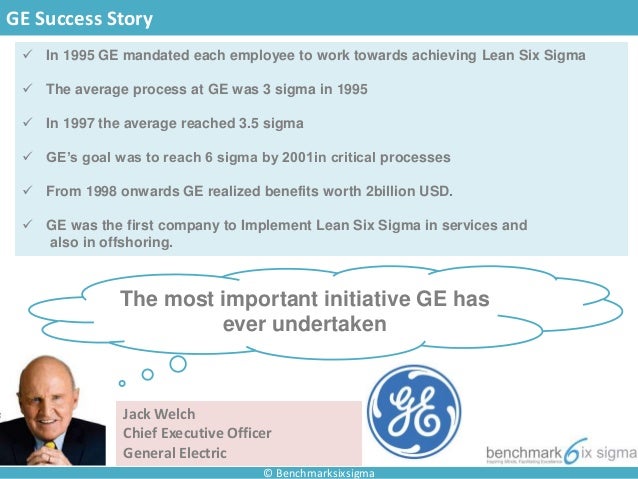

Map the value stream: Identify all the steps involved in delivering value to the customer.Define value: Understand what customers value in a product or service.It is based on five fundamental principles: Lean Manufacturing is an approach that seeks to minimize waste and maximize value in business processes. Let's start by understanding the foundations of Lean Six Sigma, its principles, history, and benefits. The primary goal of Lean Six Sigma is to create a culture of continuous improvement within an organization. Lean Six Sigma is a data-driven, structured approach to problem-solving and process improvement that combines the best of Lean Manufacturing and Six Sigma methodologies.
